Case study
How to avoid delays on your quick-turn PCBA order
How to avoid delays on your quick-turn PCBA order
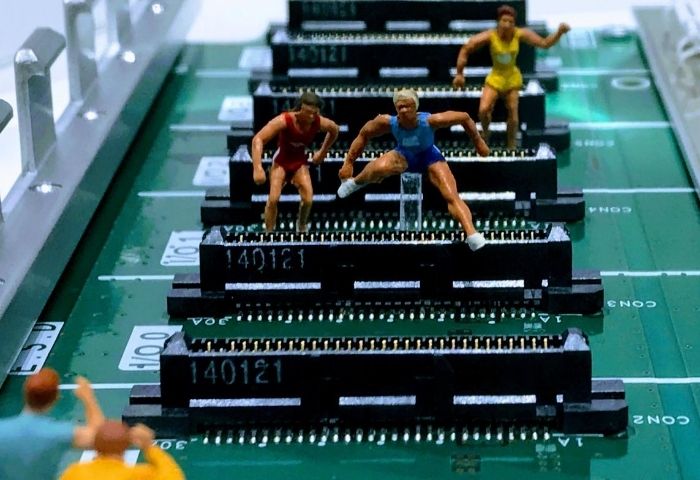
The development of modern EDA tools has greatly increased the rate of electronics development. Many engineers and project managers are adopting an iterative design approach, where development phases are planned with potential PCB updates already in mind. This has created a demand for extreme quick-turn prototype orders. CircuitHub is uniquely equipped to deal with such requirements and offers lead times as fast as 3 days. However, what can you, as a customer, do to help ensure that there are no shipping delays on your order? Here are some seemingly trivial but effective tips to avoid delays to your PCBA order. Although some of these recommendations are CircuitHub specific, many will still apply regardless of the manufacturer you are using.
Procure long lead-time components in advance
Review your bill of materials (BOM) for integrated circuits (ICs), connectors and/or other critical components as early as possible. We suggest doing this even if the layout hasn’t been completed and you’re not ready to order yet. If stock is low and lead-times are long, we recommend that you purchase your expected requirement in advance and consign it to us when you place your order.
We regularly accept consignments for many different components to mitigate the impact of component shortages. We only source from approved distributors and are subject to the same sourcing constraints as everybody else, as covered in episode 3 of the Pick, Place Podcast. If your project is complete, upload it to the CircuitHub platform, where distributor stock information is provided, via the Octopart API.
Prepare substitutes for critical or high risk components
If you haven’t had the opportunity to pre-purchase critical or high risk components that are nearing their end of life or have a global shortage, the next best thing is to prepare substitutes in advance. These can be added as alternative components per BOM line on the CircuitHub project page, under the parts section.
If the order has already been placed and we discover that a component cannot be sourced from one of our approved suppliers, we will need a substitute. We review passive components internally and substitute any that are out of stock on your behalf with ones that match or exceed the original component's specifications. For active components, we will typically need to reach out to you for a substitute or a different resolution. Specifying alternative components ahead of time helps ensure your boards are not shipped late due to last minute part substitutions.
Review the project BOM and board viewer
As soon as the project is uploaded, carry out a check on the project BOM and board viewer to make sure the BOM and imported data looks correct. It is also important to make sure that the board tab coincides with any build notes within the uploaded files. We ask that you include any specifications in your fab drawings in the "Custom Requirements" section as discrepancies between the two can lead to queries raised on our side.
Highlight requirements or issues immediately after placing your order
If you have any information about your order you would like to relay to us, post a new issue on the order page right after the order is placed. This might include a request to not fit a component, make a last minute substitute or detail specific assembly instructions. The issues can be passed on to the relevant department. There is also the ability to upload documentation to each message. Work on quick-turn orders often starts almost immediately after the order is placed, so providing any relevant information up front can prevent mistakes or delays further down the line.
Monitor your email
If we need to communicate with you about your order it will be done via the issues section of the order page. If a new issue is raised for your attention, you will receive an email notifying you of the posting. Please add the following email notifications@circuithub.com to your contacts and exclude it from any spam filters you might have. To avoid any delays to your order it is paramount that any queries we might have are answered as soon as possible.
We know how frustrating delivery delays can be, especially for time critical orders where every day makes a difference. We try to do everything under our control to make sure your orders ship on time. If you follow the prep-work steps above you can help us from running into unnecessary hurdles during the manufacturing process. For any questions about potential delays on a project we always encourage you to reach out to us using the in-browser widget or support@circuithub.com.