Case study
Formlabs improves prototyping efficiency and cuts costs with CircuitHub
Formlabs improves prototyping efficiency and cuts costs with CircuitHub
Formlabs is ubiquitous with 3D printing. The innovation they’ve brought to this 40-year old industry has made it possible for more people to have access to a 3D printer, utilize an increasing range of materials, and be able to rapidly iterate their designs.
Long-term biocompatible resin? Production-Ready Elastic 3D Printing? Castable wax resin? They've done it.
Jon Evans, Electrical Engineering Lead at Formlabs, gave us a little peek into where it all started, what the company is currently working on, and how they are continuously trying to revolutionize the manufacturing industry.
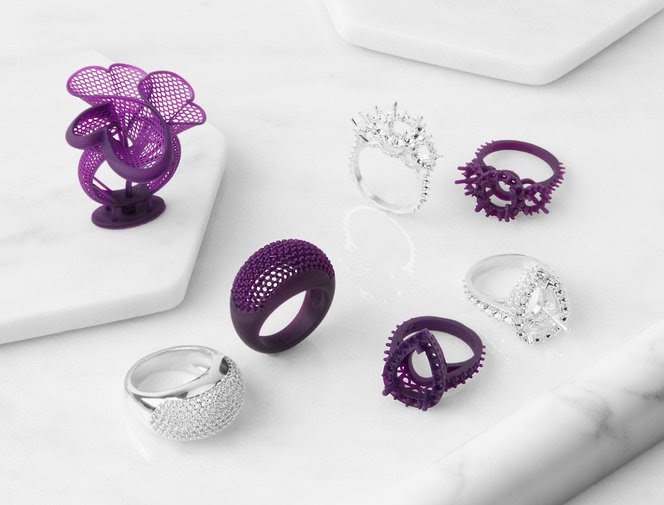
In addition to his work at Formlabs, Jon is also one of the lead developers for the open-source EDA tool, KiCad. His involvement with KiCad began after working on hobby projects at home. He noticed how expensive most commercial EDA tools were and felt compelled to contribute to KiCad in order to help create an EDA tool that is available to everyone. This principle around building accessible tools that help people do their work better and make a real difference is something deeply important to Jon and is also deep-seated in Formlabs' values.
Formlabs formed in 2011 and now has offices around the world: Germany, Japan, China, Singapore, Hungary, USA, however, a lot of the product development and prototyping still happens at their Somerville, MA headquarters. One huge benefit for the company is that they can extensively use their own printers for prototyping which in-turn, demonstrates the value of their products in rapid product development.
CircuitHub has supported Formlabs in electronic prototyping and low-volume production runs since very early on. As Jon mentioned, “The powerful web-based quoting engine that takes our native EDA files is one of the biggest benefits for us, as it allows us to place orders quickly and easily, but also to compare various options of quantity and lead time instantly and make decisions about cost trade-offs”. Traditional quoting operations slow the prototyping process down.
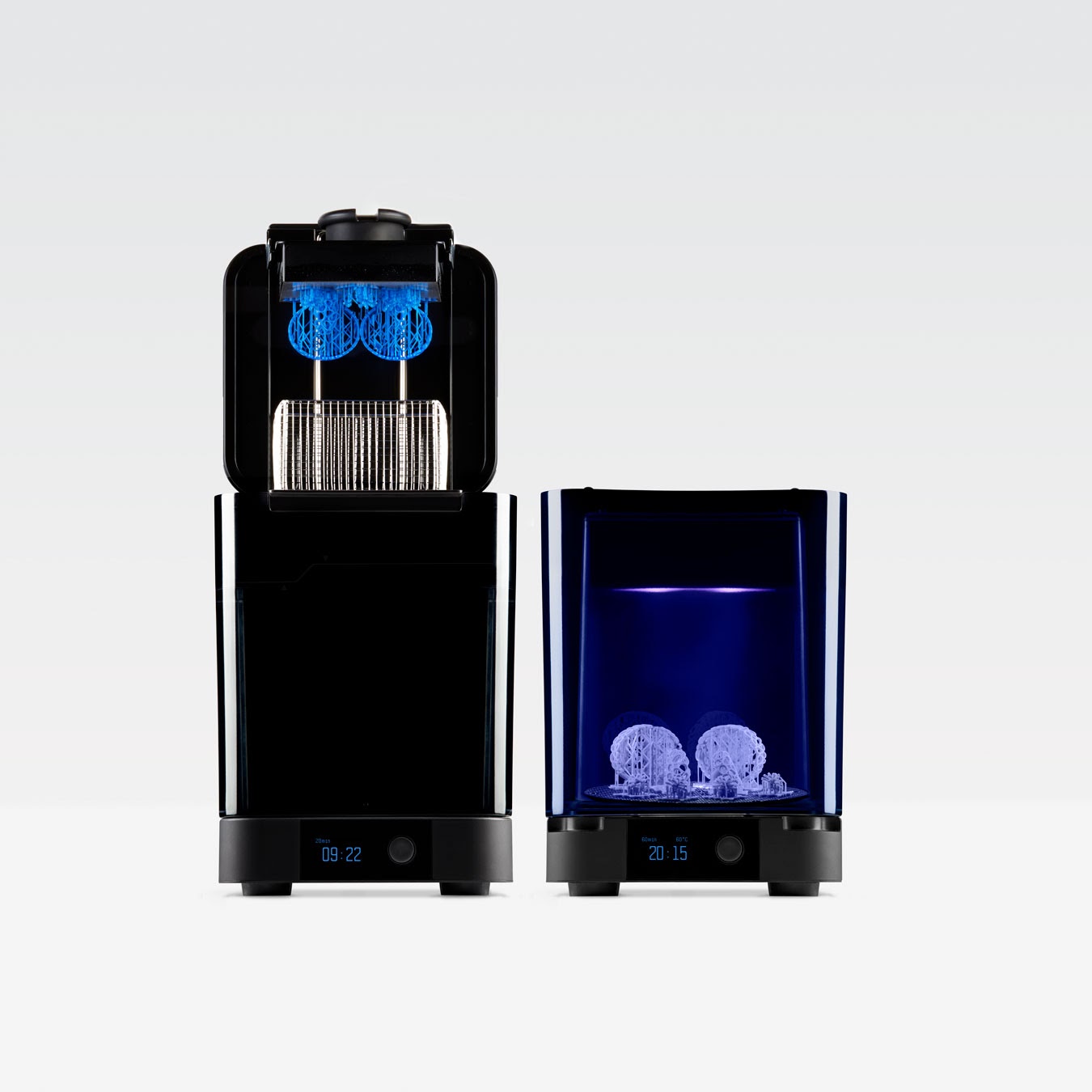
Formlabs’ first product, the Form 1, developed back in 2011, was the first affordable desktop SLA (stereolithography) 3D printer brought to market. Before it, designers had to choose between low-cost FDM printers, which produce lower-quality (resolution, surface finish) parts than SLA printers. At the time the Form 1 was released, SLA printers were generally industrial products with huge price tags, out of reach for many businesses and individuals.
SLA technology existed already, but the challenge was to design a printer that was accessible both in terms of cost and ease-of-use. Formlabs built the team with these goals in mind; engineering cost-effective mechanisms and electronics and focusing on the user experience right from the start. Since then, they have released several new SLA printers, the Form 3 being their newest model. They have also been working on new product lines, which include the Fuse 1 SLS (selective laser sintering) printer and the Form 3L large-format SLA printer.
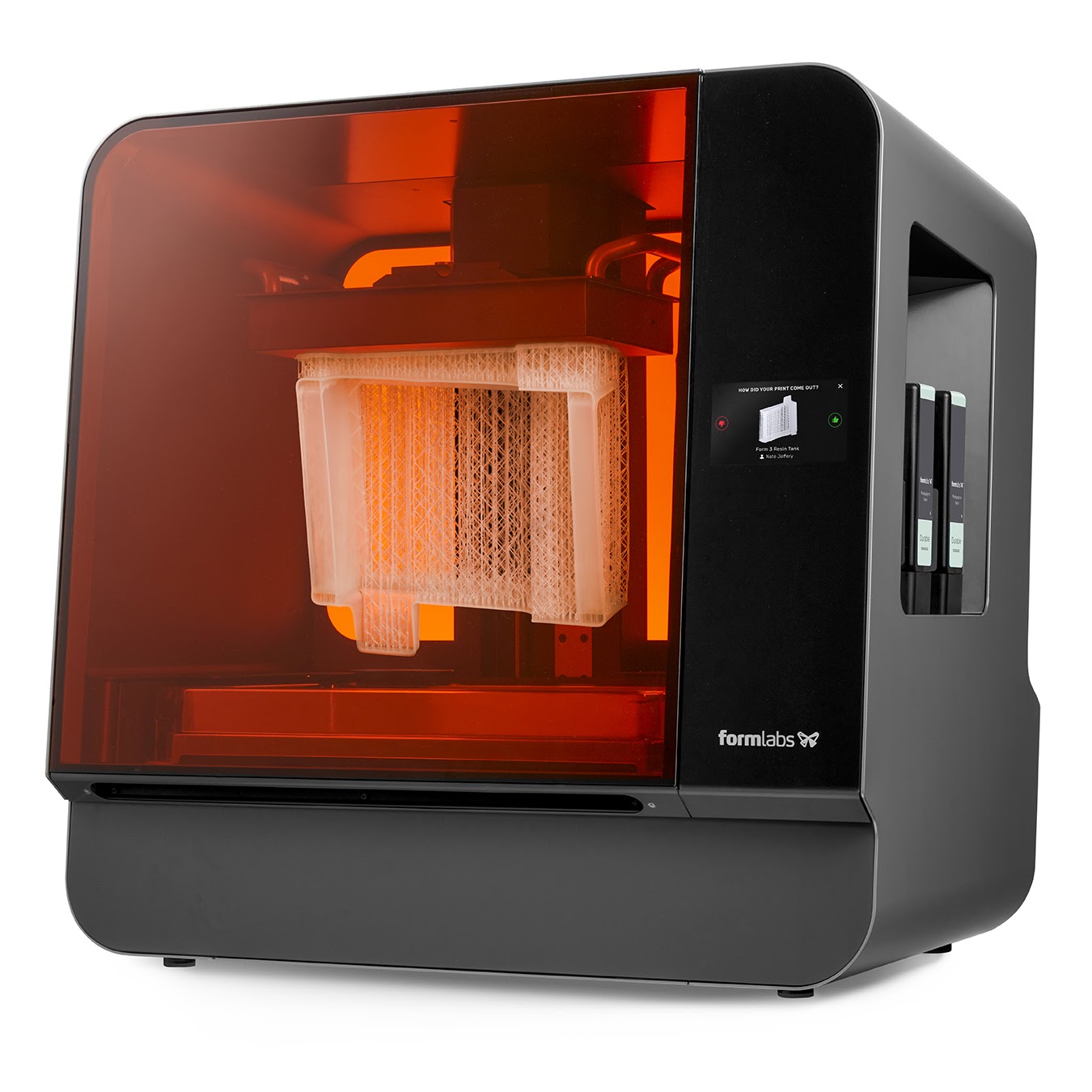
The Fuse 1 is looking to fill a gap in the SLS market, to create an industrial-quality bench-top printer at an accessible price point. While SLA uses laser to initiate a chemical reaction that cures a liquid resin, SLS uses a much more powerful laser to fuse particles of a powder material together. The Formlabs Fuse 1 sinters nylon powder to produce functional plastic parts with similar properties to injection-moulded nylon.
Currently, the Electrical Engineering team at Formlabs is responsible for developing the various electromechanical systems that go into their 3D printer products and accessories. The team's flexibility has been key in allowing them to work remotely and they have been able to easily adapt to the current global situation in order to continue their work.
To date, Formlabs has shipped more than 70,000 printers and their users have printed over 70 million parts! Their products are now used by individuals and enterprises alike in industries including product design, healthcare, dental, jewelry and education.
Check out their blog to read about some incredibly cool applications using their products. These are just a sample:
Father Helps Son With Cerebral Palsy Walk With Custom 3D Printed Orthosis
From DIY Drones to the New Frontiers of Drone Design With 3D Printing
Saving £8,000 and Two Hours of Surgery Time at the UK’s Leading Spinal Unit with 3D Printing