Case study
Getting to Know Your Manufacturer's Pick and Place Machine
Getting to Know Your Manufacturer's Pick and Place Machine
During Andrew's recent visit to Worthington Assembly he was able to have a chat with CTO Chris Denney about the benefits of using the Mydata pick and place machine over older, more traditional machines. We were impressed with Chris' knowledge and wanted to share some of what we learned about what exactly makes the Mydata machine so great.
Mydata is one of the leading suppliers of pick and place machines in the electronics industry. One of the big things that sets them apart from other pick and place manufacturers is their ability towards quick change over and flexibility.
Traditional pick and place machine feeders pull the cover tape off and spits the carrier tape out. Mydata machines do this differently by using a feeder called a plow. The cover tape goes above the plow and the carrier tape goes below the plow. The plow literally “plows” the cover tape over it; it doesn’t actually peel it off and instead just folds it over. The spent tape comes out of the back instead of the front, which helps to keep things a lot more tidy and avoids having workers step all over it. The plow is a lot easier to load in the machines than traditional feeders and provides a much more rapid setup, which is why many engineers choose manufacturers who use Mydata.
The plows have different sizes designating the amount that the cover tape will be pulled back. This allows for an increased level of accuracy when placing parts. For example a 4.7mm plow pulls the cover tape back 4.7mm. Choosing the right size is important because you don't want to peel back so much that is peels back past the glue but enough that for the part is completely exposed and can be picked up properly by the nozzle.
Each Mydata feeder has a barcode on it which lets the machine know exactly what part it has in it. The main downside is that each Mydata feeder is quite pricey, coming in at around $300. However, considering the massive decrease in set up time the price can easily be justified.
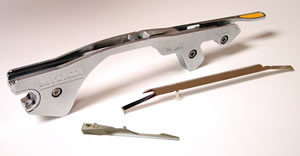
Now let's take a look at the actual machines. The old Quad machines require over 100 feeders. The machine is slow, takes long to load, is inaccurate, finicky and tends to break down a lot. The Quad machine will keep working on the boards even if it runs out of a part, which then requires a lot of time to fix after. The Mydata won't continue to build the board until you load more of that part.
The old machines are completely linear; they must build in a particular order. The Mydata machines are much more dynamic. They can mix and match the order in which they place parts on the boards depending on what is has available, what is nearby, and what nozzles it has loaded.
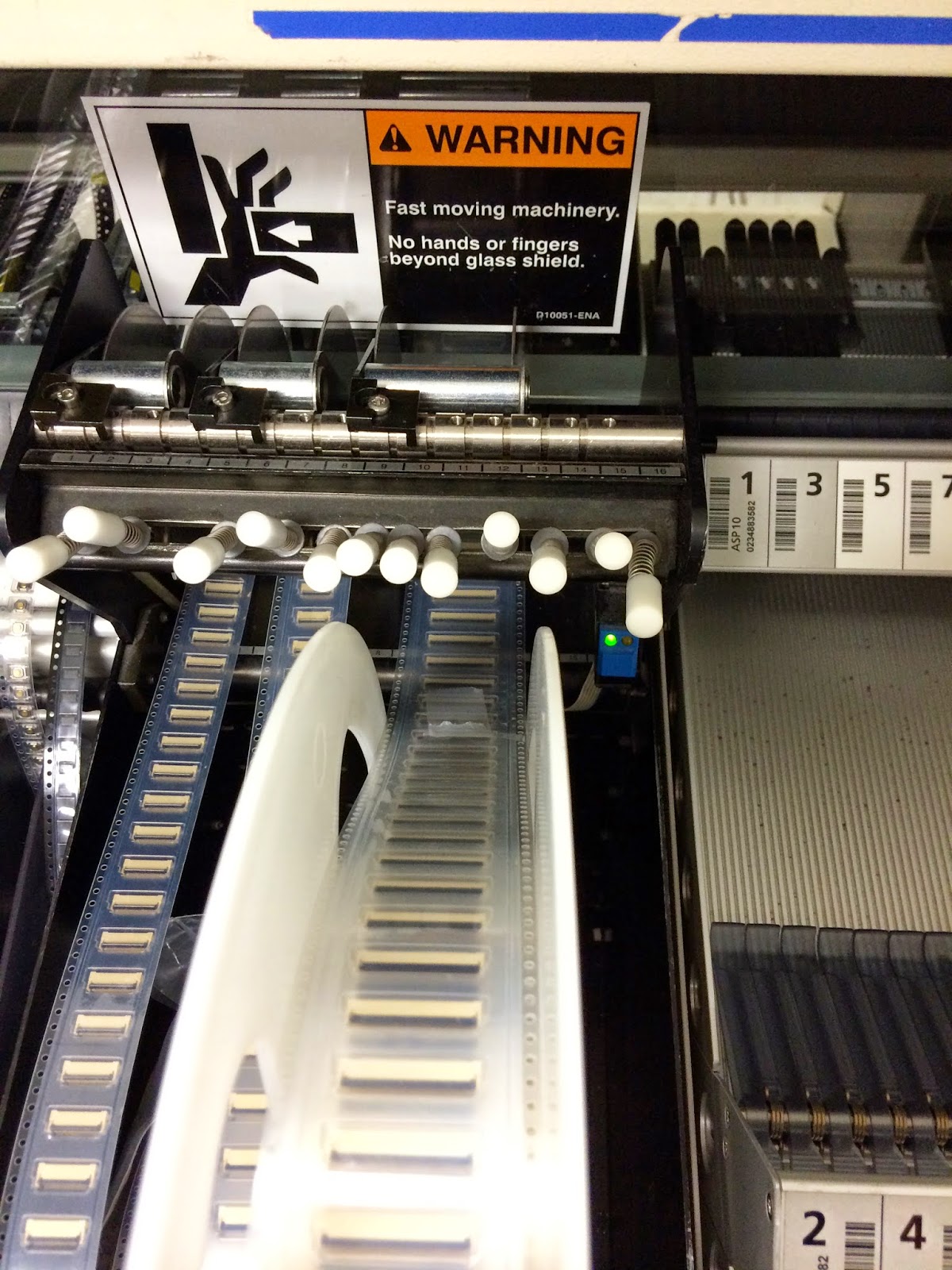
Mydata machines are capable of placing components with a very high level of accuracy. Initially you have to teach the Mydata machine the geometry of the part, and features such as leads. The neat thing is that if you want to build another batch of projects the machine already has all of the information it needs, you don't have to teach it anything. If a given part number is hooked up into the machine where all of that set up has already been done then all that is required is to marry the part number to the package.
The Mydata's flexibility and versatility has a huge effect on how CircuitHub and Worthington Assembly are able to assemble boards. As the engineering community settles around a standard set of components, we can set up dedicated feeders for them. Since the machine is already able to recognize those parts from the barcode on the feeder, all that needs to be done is to plug the feeders into the machine. This will have a drastic reduction in the setup time for a project, which for small prototype runs can take up 25% of the cost. In turn, we will be able to pass the cost savings onto you!