Case study
All About Through Hole Technology
All About Through Hole Technology
Although not as popular nowadays, through-hole components were dominant for decades. IBM pioneered the through-hole part along with printed circuits and the technology of how to put leaded components through the circuit. Before this everything was all wire wound.
IBM worked with a company called Universal Instruments, a custom machine manufacturer. IBM noticed that the shoe stapler machine had the same folding mechanism necessary for installing through-hole components and asked Universal Instruments to apply those same principles of folding staples to folding leads into a board. This is how the concept of through-hole technology all got started. These automatic insertion machines are still manufactured today by Panasonic and Universal. However, they are only really used today for boards with high volumes of through-hole, something very uncommon anymore.
Since the evolution of SMT technology has largely replaced the through-hole technology construction method, its popularity has gone way down and today are used mostly for making interconnections between board layers or when a stronger connection to the pcb is needed.
Worthington Assembly uses a machine by Contact Systems, the CS-400E, to install through-hole components. It has a contraption which is programmed to slide the board around until it locates two holes in the middle of the frame.
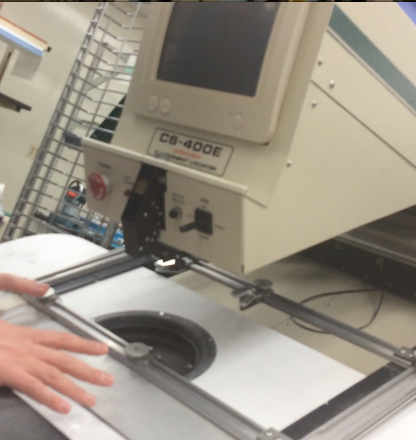
CS-400EWhen the board goes over the holes the jaws fold and cut the leads. It’s a way of getting it in there without having to do it with your fingers and hand trimmers and helps speed up the whole process. It's also more reliable because the machine only presents one part at a time so the wrong part isn't accidentally grabbed.
The technology of these machines has not changed much at all over the years. Worthington’s machine is twenty years old, but the old machines are pretty much exactly the same as the brand new ones (and works just as well). The whole system runs off of a 32 mb compact flash DOS software and is backed up onto a floppy.
The machine doesn’t solder the components, it is just for putting the leads in. For soldering though-hole components, a selective soldering machine is used. Worthington uses a machine manufactured by RPS Automation (2010 Rhythm model). If you're interested, Chris Denney wrote a series of articles on tips and tricks for using a selective solder machine.
Here's what WAi's selective soldering machine looks like in action:
If there are other components on the board located too close to the through-holes the selective soldering machine cannot be used and must be soldered by hand. In order to avoid hand soldering your should use a 2mm minimum clearance all the way around your through-holes.
Because through-hole components require additional setup and time they can significantly increase the assembly cost of a board. Unless you have a specific reason for including them, it's best to stick to surface mount. It will make your wallet happy and the assembly house :)